Sait Abrasives Case Study in Leicester
Sait Abrasives needed a heating solution for the premises where they manufacture and store their products.
Sait Abrasive’s Problem
Sait Abrasives is one of the most important companies on the European and Global scene for producing rigid and flexible abrasives for industrial use. OKEL was first contacted by Sait Abrasives in July 2019, looking to upgrade the heating system within their large open-plan premises used for both manufacturing and storage of abrasives products.
At the time, they were heating the premises with five obsolete natural gas-fired warm air heaters, two of which were no longer operational and an old, no longer effective destratification system at ceiling height. Due to natural aged-related wear and tear, the now obsolete system was no longer providing them with the reliability and efficiency required and replacement components were becoming difficult to source when repairs were necessary. It was also important for the quality of the abrasives stored on the premises that the temperature did not fall below 10°C.
OKEL Solution
OKEL attended the site to meet with Sait Abrasives’s Managing Director to fully understand the heating requirements and to complete a detailed heating survey of the premises.
Considering all the findings from the survey, OKEL recommended that Sait Abrasives introduce a high-efficiency wall-mounted warm air and destratification heating solution that would be fuelled by the existing natural gas supply and would consist of 4 x 60 kW fully modulating suspended warm air heaters with integral axial fans.
To support the heater’s integral axial fans, OKEL’s design introduced 8 standalone destratification fans to be evenly spread at ceiling height. Destratification works by recognising when the temperature gradient becomes too hot at ceiling height and forces the warm air back down to the lower level where it’s of most benefit.
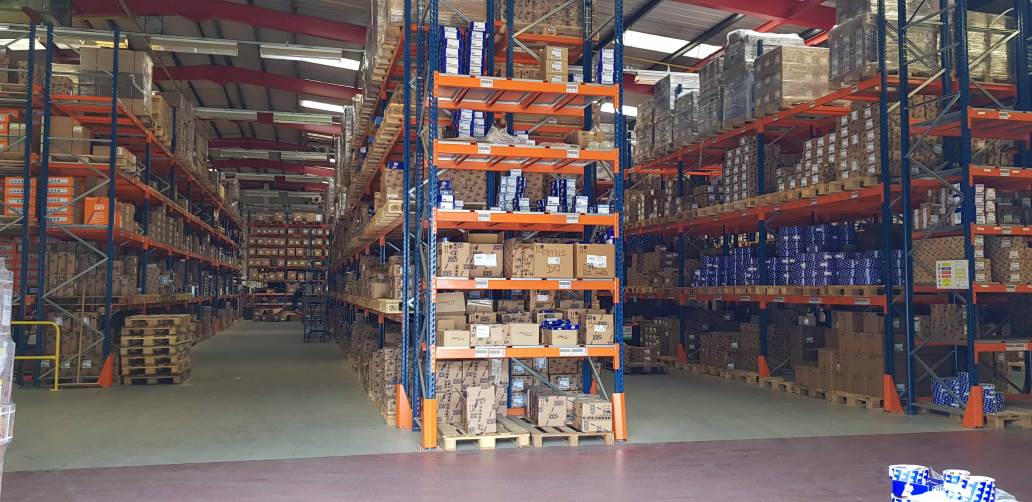
Added Benefits
Destratification can also provide summer ventilation when the outside temperatures start to rise helping to deliver a flow of cooler air in the warmer summer months. The Carbon Trust estimates that the use of destratification fans in industrial buildings with high ceilings and operating a warm air heating system can reduce energy consumption by a further 20%.
To ensure the warm air heaters delivered optimum performance they would be individually controlled by a multi-functional thermostatic controller which offers frost protection, keyboard locking, overtime programme, 10 programmable time blocks, summer ventilation mode and the facility to connect to a BMS system.
An expertly designed warm air and destratification system can reduce energy consumption by up to
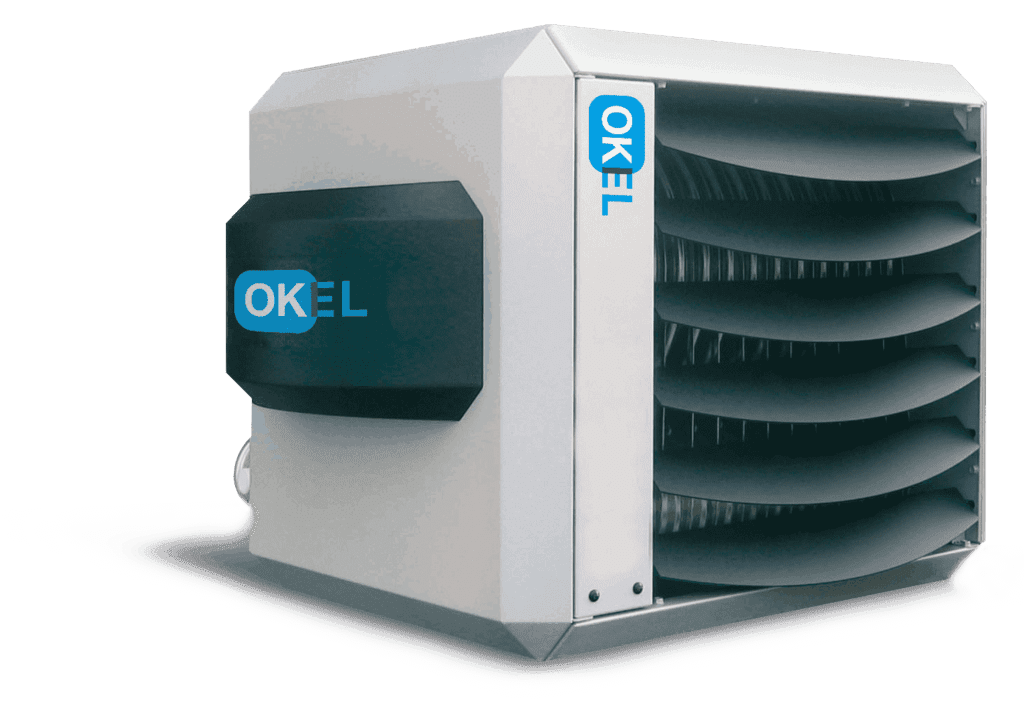
Sait Abrasive’s Results
The positioning of the heaters was agreed between our client and lead engineer to determine the most even spread of heat whilst taking into consideration our client’s preferences.
The installation was completed in September 2019 and upon project completion, Sait Abrasives received a full handover to ensure staff were confident in the capabilities of the heaters and able to maximise the efficiencies by effective use of the intelligent thermostatic heater controls. Electronic Gas Safe commissioning certification was forwarded to our client on project completion.
All works were completed by our chosen team of commercial gas-safe heating engineers and included the decommissioning and taking down of the obsolete heaters.
The installation was completed in September 2019 and upon project completion our client received a full handover to ensure staff were confident on the capabilities of the heaters and able to maximise the efficiencies by effective use of the intelligent thermostatic heater controls. Electronic Gas Safe commissioning certification was forwarded to our client on project completion.